PCB Assembly Equipment
ANKE PCB offers a large selection of SMT equipment including manual, semi-automatic and fully automatic stencil printers, pick&place machines as well as benchtop batch and low to mid-volume reflow ovens for surface mount assembly.
At ANKE PCB we fully understand quality is the primary goal of PCB assembly and able to accomplish the state-of-the-art facility that comply the latest PCB fabrication and assembly equipments.
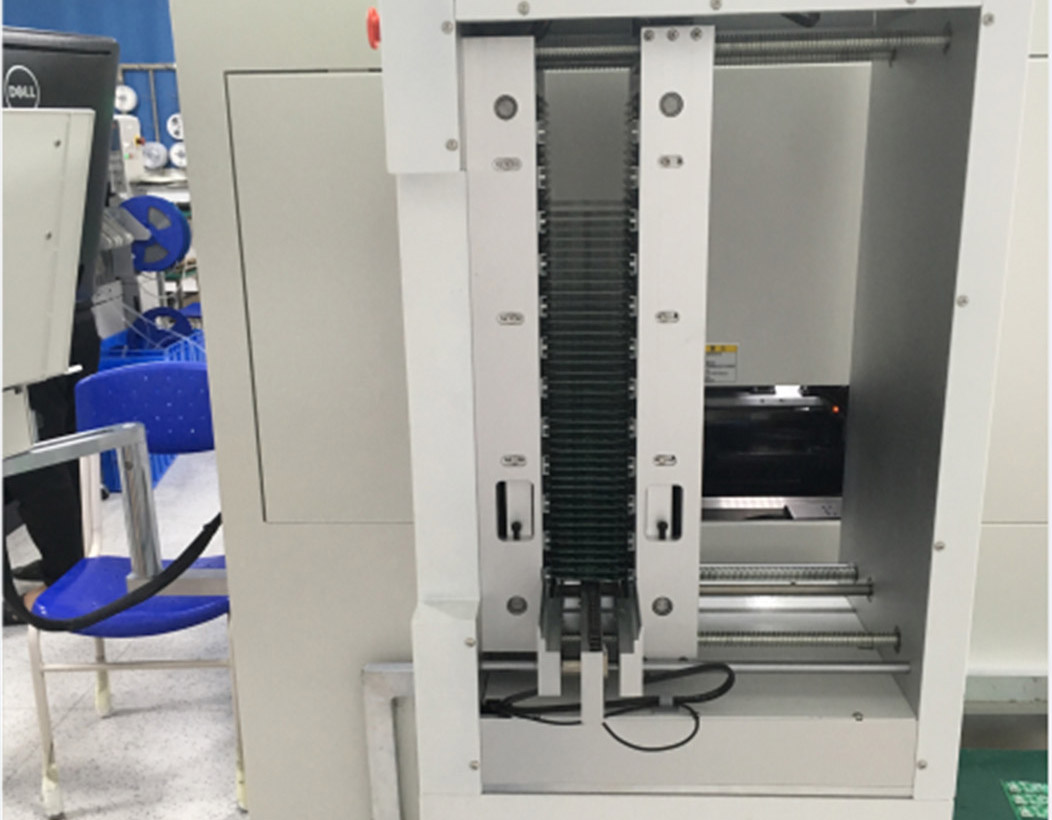
Automatic PCB loader
This machine allows pcb boards to feed into the automatic solder paste printing machine.
Advantage
• Time saving for labor force
• Cost saving in assembly production
• Decreasing the possible fault that will be caused by manual
Automatic Stencil Printer
ANKE has advance equipment such as automatic stencil printer machines.
• Programmable
• Squeegee system
• Stencil automatic position system
• Independent cleaning system
• PCB transfer and position system
• Easy-to-use interface humanized English/Chinese
• Image capture system
• 2D inspection & SPC
• CCD stencil alignment
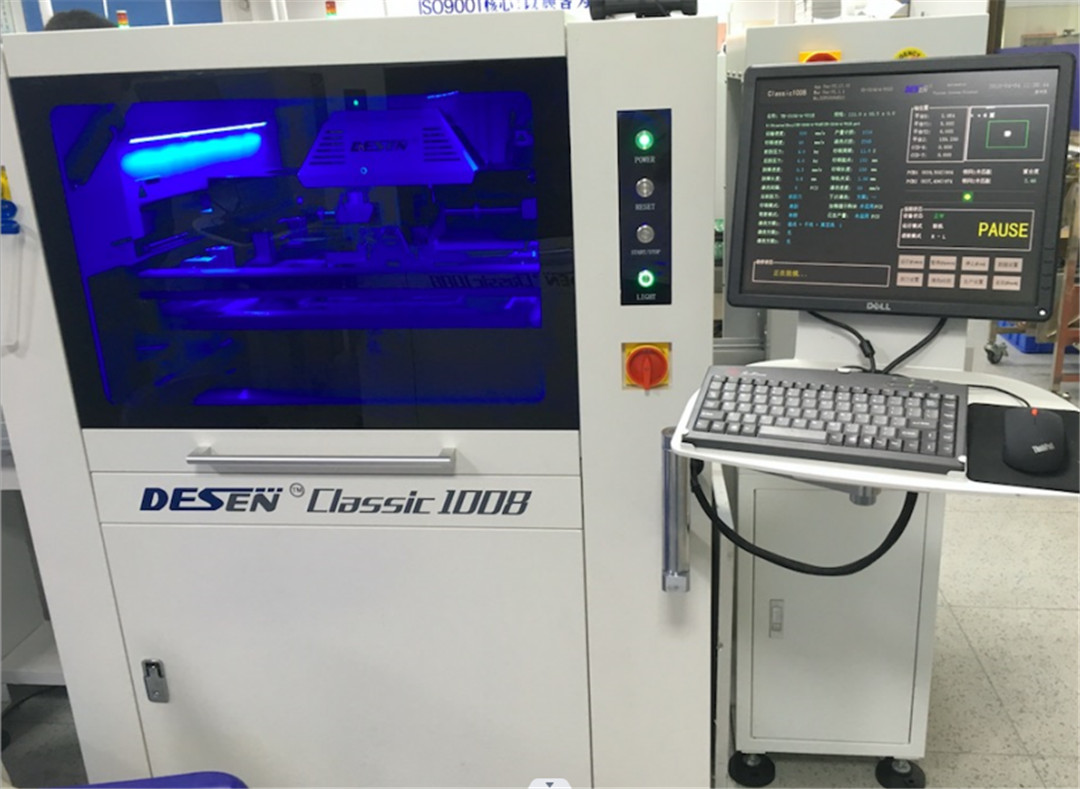
SMT Pick&Place Machines
• High accuracy and high flexibility for 01005, 0201, SOIC, PLCC, BGA, MBGA, CSP, QFP, up to fine-pitch 0.3mm
• Non-contact linear encoder system for high repeatability and stability
• Smart feeder system provides automatic feeder position checking, automatic component counting, production data traceability
• COGNEX alignment system "Vision on the Fly"
• Bottom vision alignment system for fine pitch QFP & BGA
• Perfect for small & medium volume production
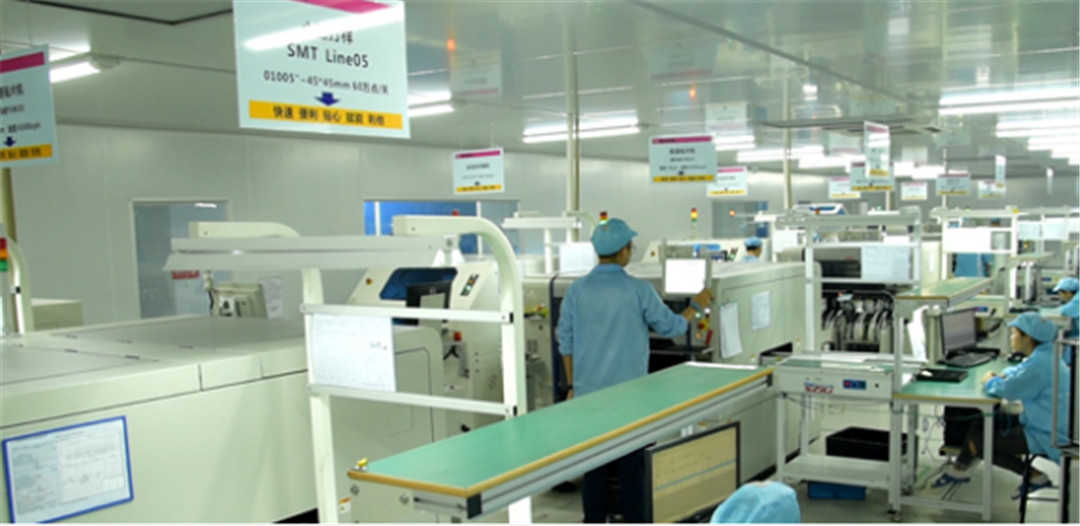
• Built-in camera system with auto smart fiducial mark learning
• Dispenser system
• Vision inspection before and after production
• Universal CAD conversion
• Placement rate: 10,500 cph (IPC 9850)
• Ball screw systems in X- and Y-axes
• Suitable for 160 intelligent auto tape feeder
Lead-Free Reflow Oven/Lead-Free Reflow Soldering Machine
•Windows XP operation software with Chinese and English alternatives. The whole system under
integration control can analyze and display the failure. All production data can be saved completely and analyzed.
• PC&Siemens PLC controlling unit with stable performance; high precision of profile repetition can avoid product loss attributed to the abnormal running of the computer.
• The unique design of the thermal convection of the heating zones from 4 sides provides high heat efficiency; the high-temperature difference between 2 joint zones can avoid temperature interference; It can shorten the temperature difference between big-size and small components and meet the soldering demand of complex PCB.
• Forced air cooling or water cooling chiller with efficient cooling speed suits all different kinds of lead free soldering paste.
• Low power consumption (8-10 KWH/hour) to save the manufacturing cost.
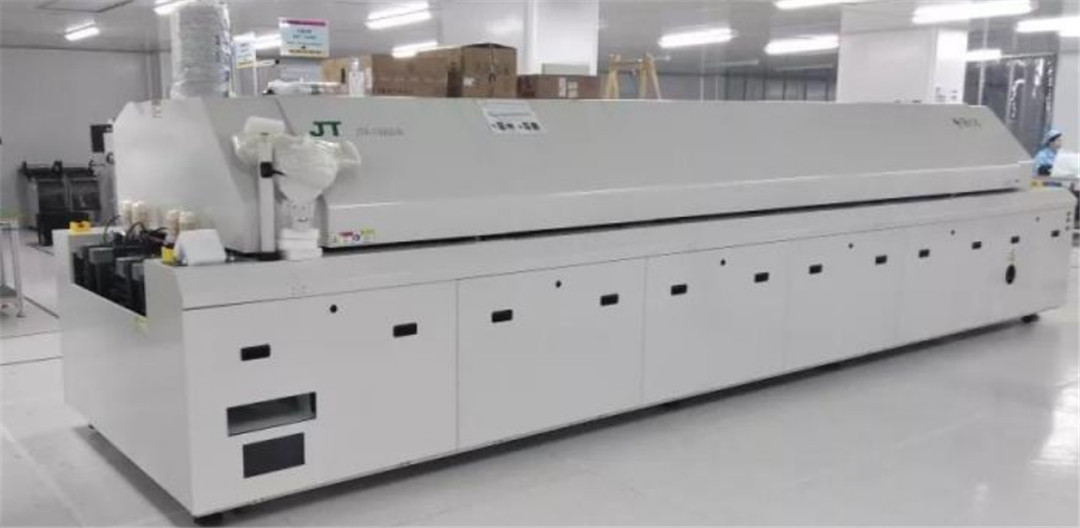
AOI (Automated Optical Inspection System)
AOI is a device that detects common defects in welding production based on optical principles. AOl is an emerging testing technology, but it is developing rapidly, and many manufacturers have launched Al testing equipment.
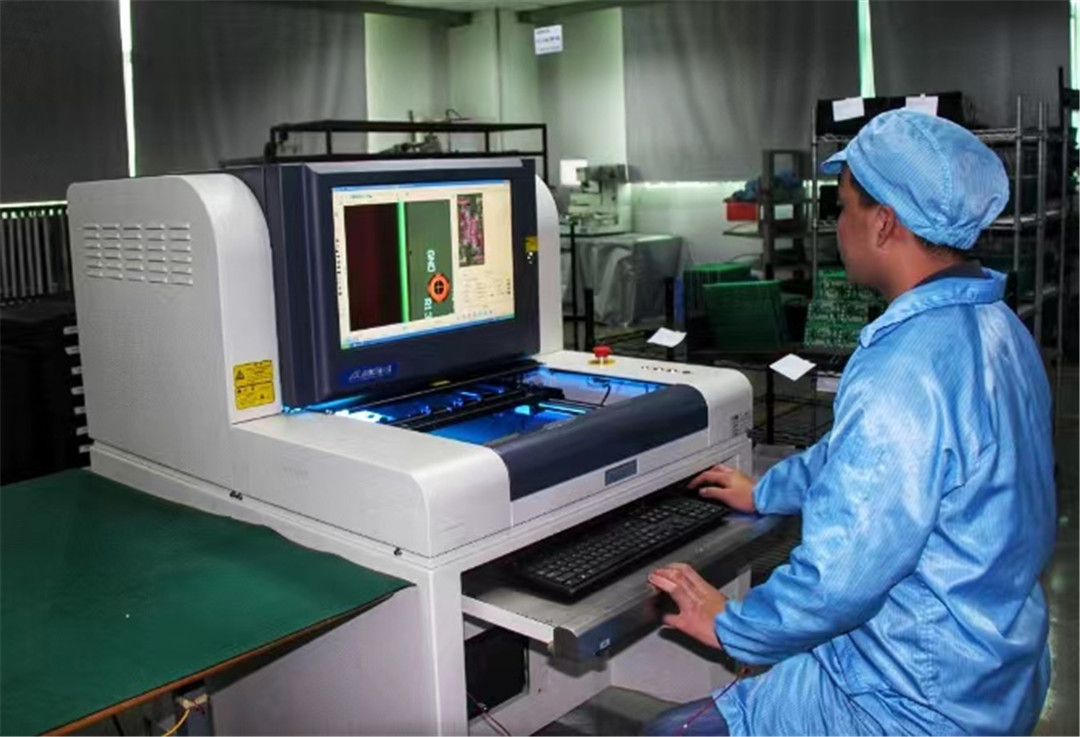
During automatic inspection, the machine automatically scans the PCBA through the camera, collects images, and compares the detected solder joints with the qualified parameters in the database. Repairman repairs.
High-speed, high-precision vision processing technology is used to automatically detect various placement errors and soldering defects on the PB board.
PC boards range from fine-pitch high-density boards to low-density large-size boards, providing in-line inspection solutions to improve production efficiency and solder quality.
By using AOl as a defect reduction tool, errors can be found and eliminated early in the assembly process, resulting in good process control. Early detection of defects will prevent bad boards from being sent to subsequent assembly stages. AI will reduce repair costs and avoid scrapping boards beyond repair.
3D X-Ray
With the rapid development of electronic technology, the miniaturization of packaging, high-density assembly, and the continuous emergence of various new packaging technologies, the requirements for circuit assembly quality are getting higher and higher.
Therefore, higher requirements are placed on detection methods and technologies.
In order to meet this requirement, new inspection technologies are constantly emerging, and 3D automatic X-ray inspection technology is a typical representative.
It can not only detect invisible solder joints, such as BGA (Ball Grid Array, ball grid array package), etc., but also conduct qualitative and quantitative analysis of the detection results to find faults early.
Currently, a wide variety of test techniques are applied in the field of electronic assembly testing.
Commonly equipments are Manual visual inspection (MVI), In-circuit tester (ICT), and Automatic Optical
Inspection (Automatic Optical Inspection). AI), Automatic X-ray Inspection (AXI), Functional Tester (FT) etc.
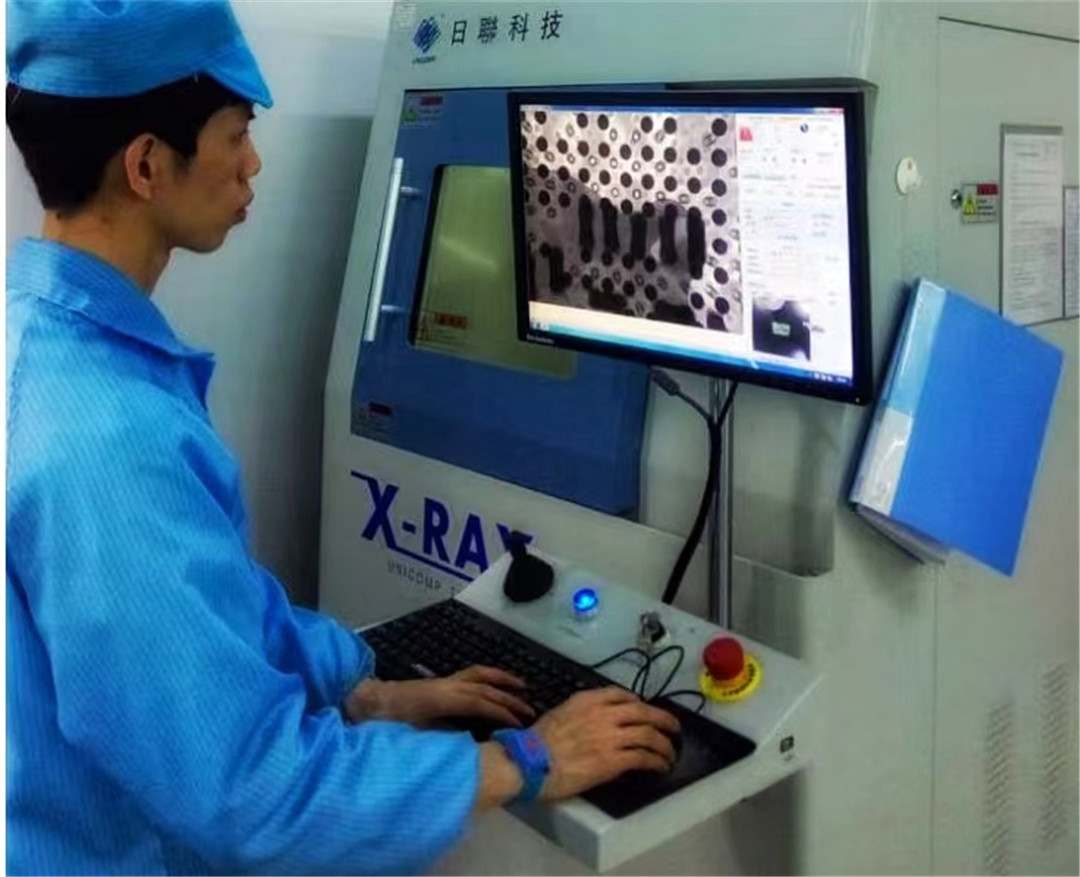
PCBA Rework Station
As far as the rework process of the entire SMT assembly is concerned, it can be divided into several steps such as desoldering, component reshaping, PCB pad cleaning, component placement, welding, and cleaning.
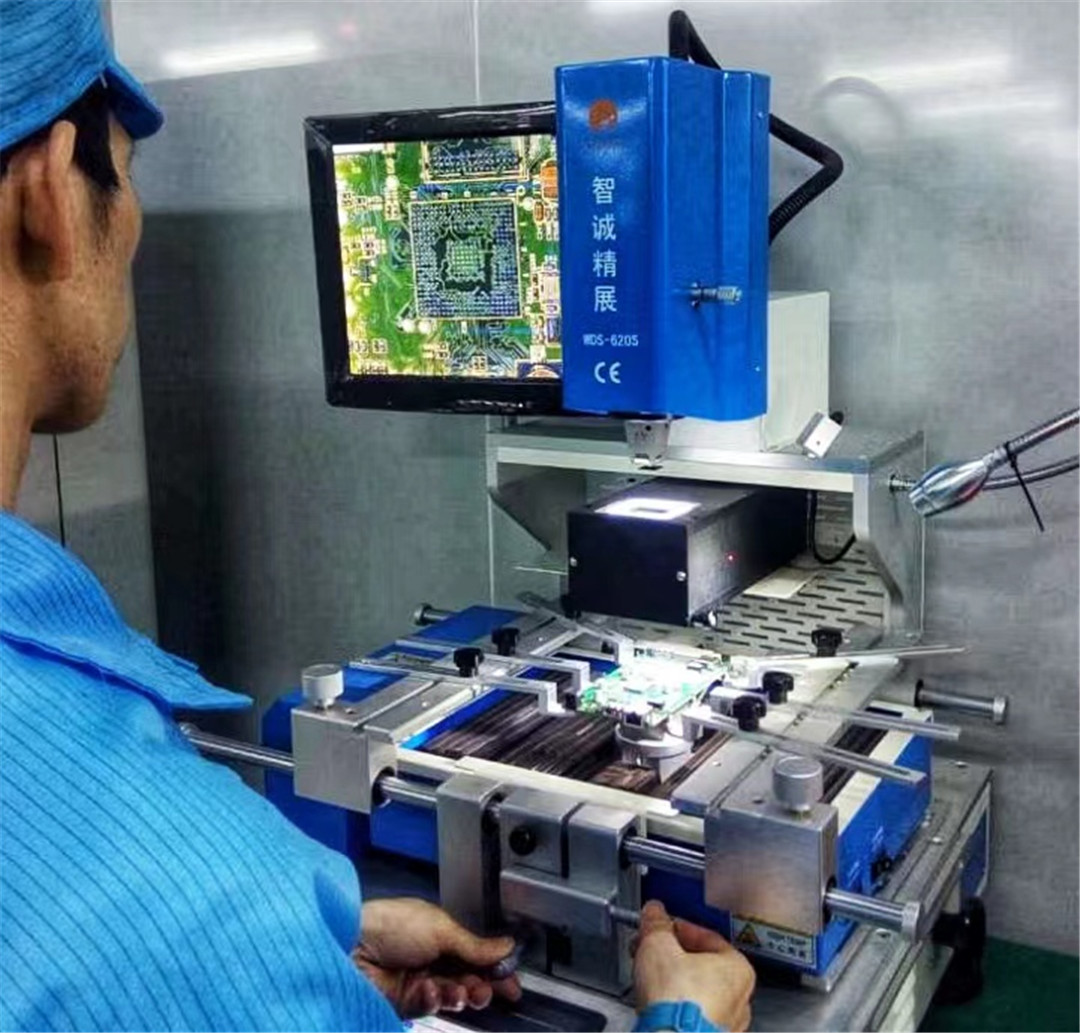
1. Desoldering: This process is to remove the repaired components from the PB of the fixed SMT components. The most basic principle is not to damage or damage the removed components themselves, surrounding components and PCB pads.
2. Component shaping: After the reworked components are desoldered, if you want to continue to use the removed components, you must reshape the components.
3. PCB pad cleaning: PCB pad cleaning includes pad cleaning and alignment work. Pad leveling usually refers to the leveling of the PCB pad surface of the removed device. Pad cleaning usually uses solder. A cleaning tool, such as a soldering iron, removes residual solder from the pads, then wipes with absolute alcohol or an approved solvent to remove fines and residual flux components.
4. Placement of components: check the reworked PCB with the printed solder paste; use the component placement device of the rework station to select the appropriate vacuum nozzle and fix the rework PCB to be placed.
5. Soldering: The soldering process for rework can basically be divided into manual soldering and reflow soldering. Requires careful consideration based on component and PB layout properties, as well as the properties of the welding material used. Manual welding is relatively simple and is mainly used for rework welding of small parts.
Lead-Free Wave Soldering Machine
• Touch screen + PLC control unit, simple and reliable operation.
• External streamlined design, internal modular design, not only beautiful but also easy to maintain.
• The flux sprayer produces good atomization with low flux consumption.
• Turbo fan exhaust with shielding curtain to prevent the diffusion of atomized flux into the preheating zone, ensuring safe operation.
• Modularized heater preheating is convenient for maintenance; PID control heating, stable temperature, smooth curve, solve the difficulty of lead-free process.
• Solder pans using high-strength, non-deformable cast iron produce superior thermal efficiency.
Nozzles made of titanium ensure low thermal deformation and low oxidation.
• It has the function of automatic timed startup and shutdown of the whole machine.
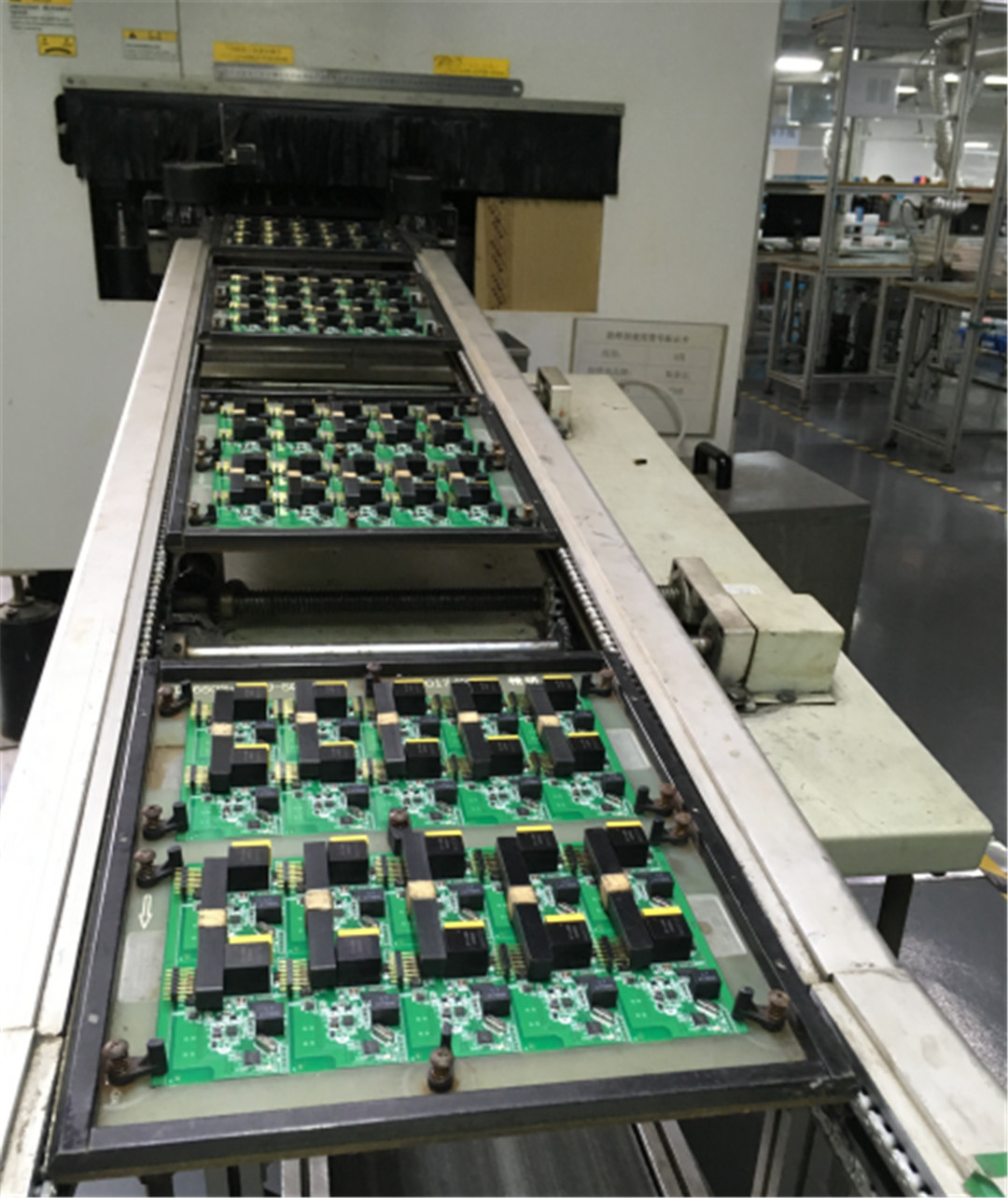